General Guidelines
Wall Thickness
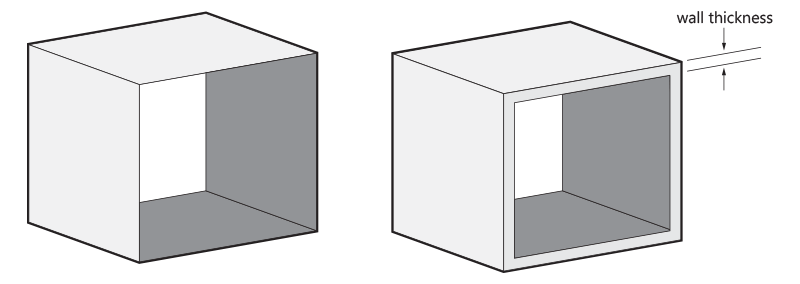
High Definition
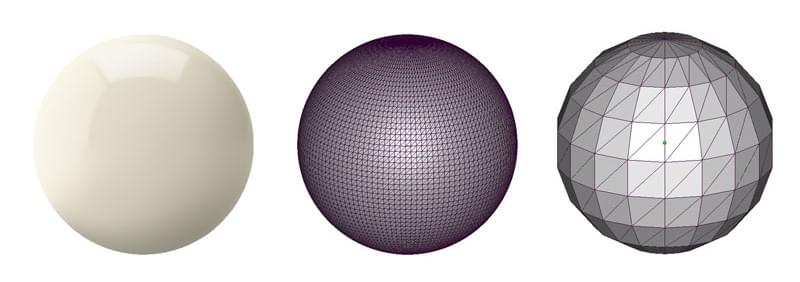
Since the resolution of the wax printing process is so high, make sure that you create your model and export your file with enough definition so you don’t see the triangles.
Geometry
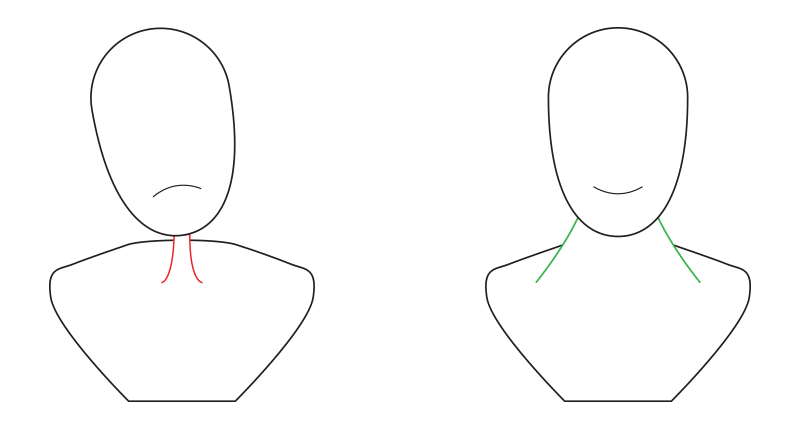
Be careful when having large areas of your model connected supported by thin rods. Compare it to a big head resting on a thin neck. Ask yourself if the rods are strong enough to ‘carry’ the weight of the larger area. Also, internal structures are possible to print, but removing support structures, cleaning them and casting them can be difficult or even impossible. If you have doubts about whether your model is feasible, please contact us.
Hollow Models
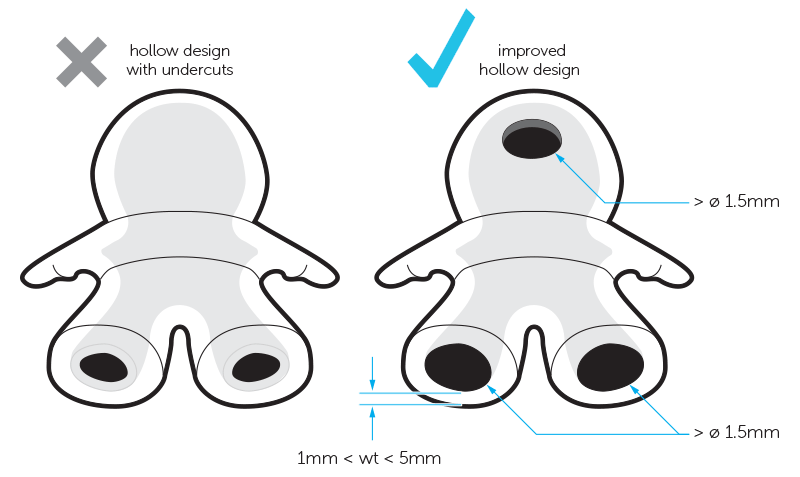
This material allows you to print hollow models. However, keep in mind that you need to incorporate multiple holes or slots so that we can get rid of any unprinted wax resin. In addition, you will need to make sure that the casting plaster is sufficiently supported or your model will not be able to be cast properly. Make as many holes or slots as you possible can. We recommend making two or more holes or slots. Make sure the holes are spread out equally; for example on opposite ends of your design. The holes should have a diameter larger than 1.5 mm.
Feature Size
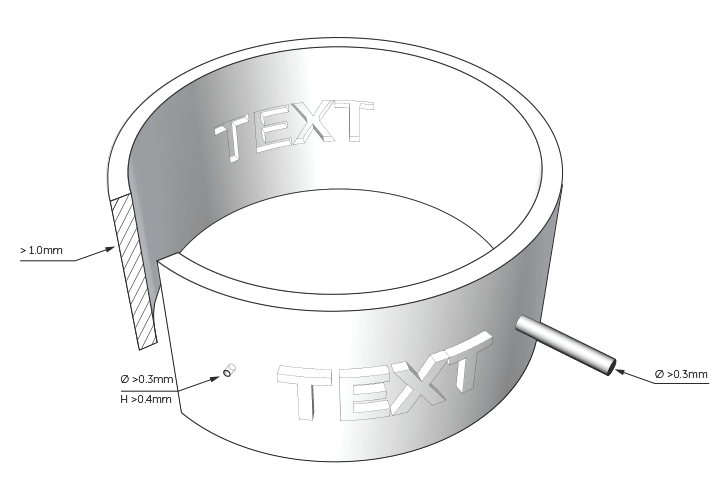
The smallest features in your design should be at least 0.35 mm in diameter and 0.4 mm in height and attached to a solid surface. Details this small are suitable for delicate projects such as micro pavé settings.
Because Silver is not a very strong material, longer features such as rods or prongs (in mesh-like structures) should be at least 0.8 mm in diameter. Otherwise, they might break during casting or even when you wear the piece.
Clearance
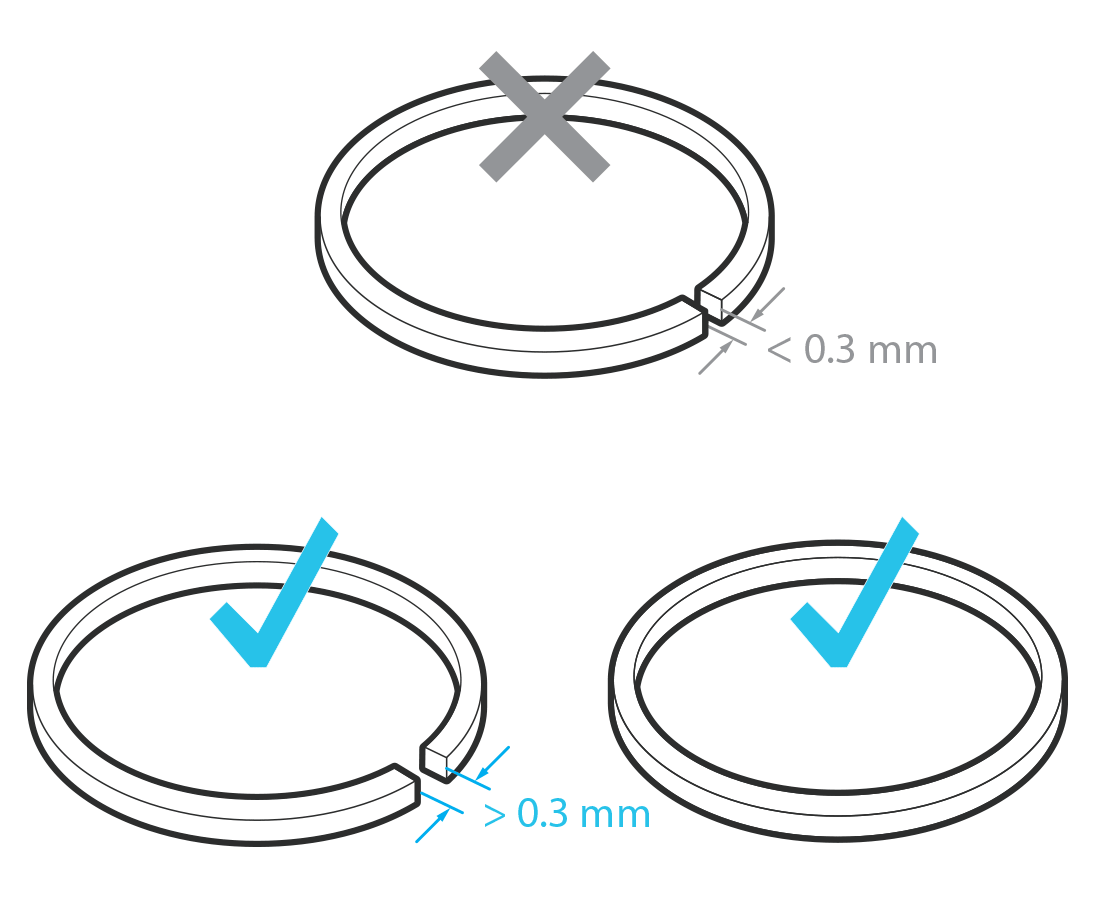
Polishing
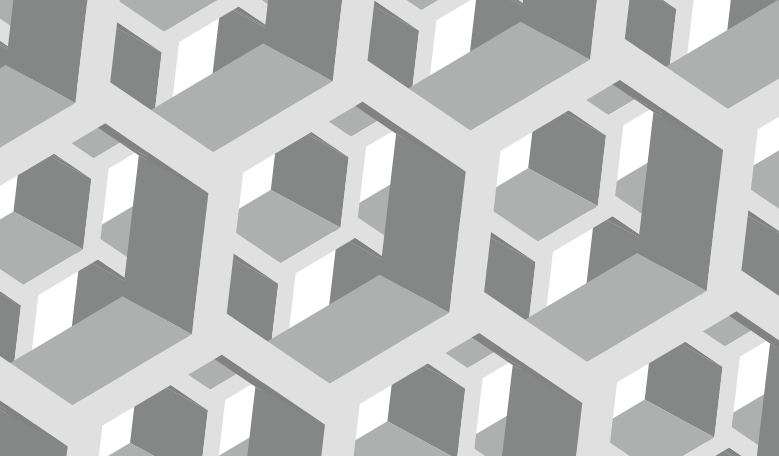
In order to polish, we have to be able to reach the surfaces. As a rule, we can't file, sand or polish cavities and small sharp edges will be rounded off. Also, as you can imagine, complex internal, mesh-like structures are also impossible to reach.
Finishing and Its Influence on the Level of Detail
Once your model is cast it will go to finishing. The post-processing techniques for gloss, satin, sandblasted and high gloss silver are all unique and each will have a different effect on your model’s level of detail.
- Gloss models are post-processed in a magnetic tumbler. This technique is the least aggressive process for silver and will erode your model by about 0.05 mm to 0.075 mm. This finish is best suited to maintain a high level of detail; however, surfaces will be left uneven and not as smooth as high-gloss models.
- Sandblasted models are post-treated with an abrasive blasting operation. The surfaces of your model will get a smooth, matt look. This finish will erode your model by about 0.10 to 0.15 mm.
- Satin models are manually post-treated with a wire brush. This finish will eat away 0.10 to 0.15 mm of material from your model.
- High Gloss models will undergo a manual mechanical polish. The polishing technique is the most aggressive and will erode your model by about 0.10 to 0.15 mm. Sharp corners will be rounded. Therefore, this technique will result in the lowest level of detail for Silver but provides the highest level of smoothness and shine.
- Antique models undergo a manual mechanical polish. This polishing technique is the most aggressive; it will erode your model’s outer surfaces by approximately 0.10 to 0.15mm and will round sharp corners. Therefore, this technique results in the lowest level of detail for silver but provides the highest level of smoothness and shine.
It’s good to take the amount of erosion from these finishes into account when you are designing your model.
Nested Objects, Hinged and Interlinking Parts
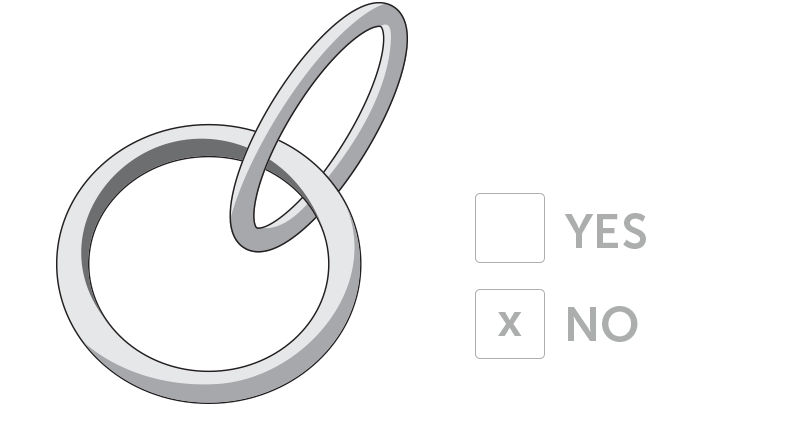
Nested objects (objects floating within another object), hinged parts, and interlinking parts, such as chains, or copies / parts within the same file e.g. earrings, cannot be made with lost wax casting. The reason is that support structures have to be removed before being cast in Silver.
Engraved Text and Surface Details
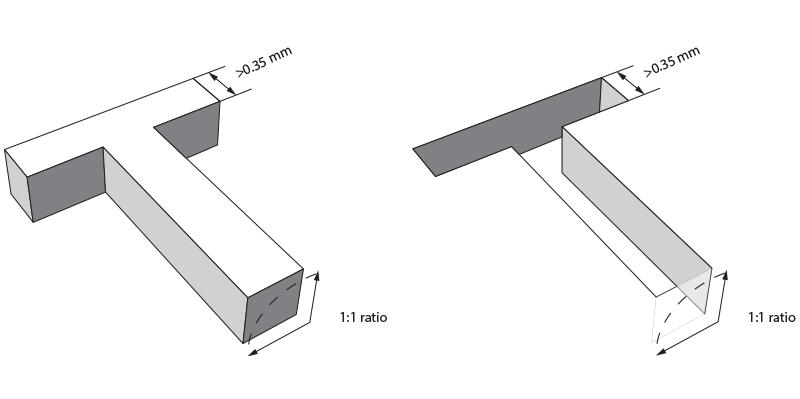
For embossing or engraving details such as text, we advise you to keep a maximum height/depth-to-width ratio of 1:1. Also, keep in mind the minimum wall thickness of 0.35 mm.
Guidelines for Antique Models
Antique models are finished in 2 steps. First your model will be undergo an oxidation process: a sulfur mixture causes the silver to become duller and darker. Then, the elevated surfaces of your model are polished manually. Recessed or sunken areas are left untouched and therefore stay darker than the elevated, polished areas.
Minimal Dimensions of Sunken “Darker” Areas
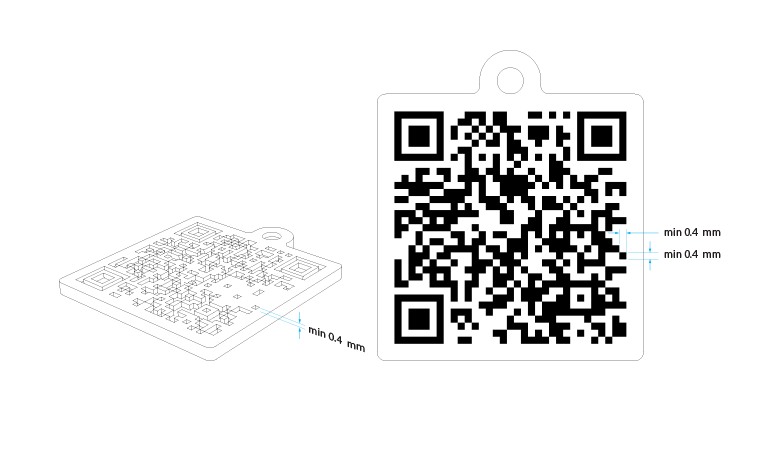
Sunken areas need to have a minimum area of 0.4 mm long x 0.4 mm wide x 0.4 mm high to give visible results. Because the final polishing is a manual process, each model will be unique.