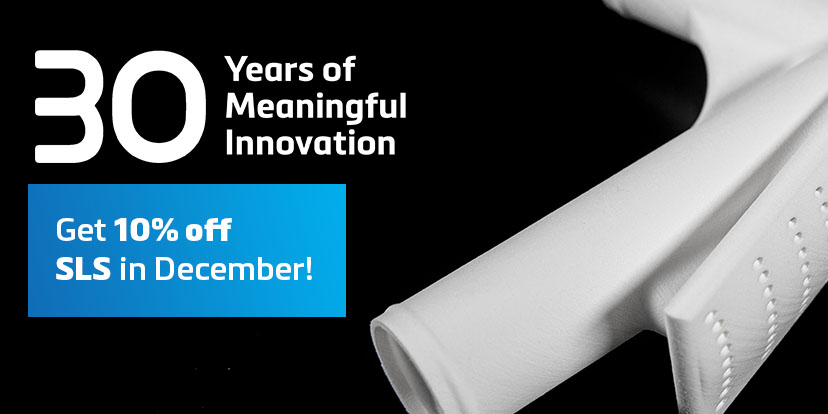
30 Years Of Innovation: Dependable SLS Enables Sustainability In AM
We’re wrapping up our 30th-anniversary blog series for our parent company, Materialise, with a look at the final 3D printing technology in our portfolio: selective laser sintering (SLS). SLS, with i.mat offerings in Polyamide (SLS), Alumide, and Polypropylene, has been offered at Materialise since 1998. Over the past 22 years, our team has worked with this technology to reliably print application after application. This next decade, we’re turning our sights on sustainability, and SLS has a major role in enabling our customers to order prints that are manufactured in a more sustainable way with our new Bluesint PA12 material.
Selective laser sintering is a popular and versatile 3D printing method that uses — you guessed it — lasers to bind powder particles together. Because of its adaptable process and high-quality output, SLS works well with a wide range of applications, from prototyping to series production.
A Favorite In The Industry
SLS is used quite frequently in 3D printing — and for good reason. As an affordable, quick, and accurate technology, it checks off many boxes and is a great option for serial production.
“One advantage of SLS is its productivity. Because parts are printed in a power bed, no support structures are needed, and you can really optimize each build to its fullest. This is especially useful in series manufacturing because you can print many copies of the same part in one go.
“Another benefit is the quality of the parts. SLS parts have very good mechanical properties compared to injection-molded parts of the same material. SLS creates robust parts,” explains Giovanni Vleminckx, Research Project Manager at Materialise.
Laser sintering’s advantages also bring great value to prototyping.
“On top of these other capabilities, SLS is fast, which is crucial for prototyping. Having the ability to nest many parts in the same build means that you can use one run of the machine for one-off parts, often prototypes, from various customers if they are the same material,” says Giovanni. “This chips down the lead time and decreases the cost because you can spread the cost of your single run among more parts. AM is fantastic for rapid prototyping, and that value really shines through with SLS.”
SLS Wears Many Hats
SLS is the technology behind our Polyamide, Alumide, and Polypropylene materials. It’s a versatile, reliable option, making it an excellent match for many applications, ranging from a queen’s crown to fossil models to eyewear.
Laser sintering’s usefulness is proven in both one-of-a-kind projects and repeat series. Its capabilities, such as the ability to print hinges and interlocking parts, allow designers to look at traditional products through a different lens. An example of this is the beautiful 2.7-meter wedding veil shown above. In addition to this mobility, SLS was chosen because the wedding veil could be printed folded over itself within the powder bed to create the length.
In mass production instances, SLS shows its value in applications like eyewear. At Materialise, laser sintering is often our go-to for eyewear applications for its high quality and ability to print many parts in one build. Plus, SLS provides the style and reliability that consumers need in their eyewear thanks to a wide variety of colors and finishes, impressive mechanical properties, and skin contact safety that will last throughout the accessory’s lifetime.
A New Material Enables Sustainable Choices
Back in 2014, our team questioned how we could make SLS more sustainable. The powder used during this process could be recycled, but only when combined with fresh material. That means that only about 50% of each build can be recycled powder. The rest of the used powder, unfortunately, goes to waste.
So, backed by the European Commission and VLAIO, we began tweaking laser sintering to develop a reliable process using 100% reused powder. And 6 years later, we can finally share it with the world in the form of our new material currently in the validation process that enables us to print parts using a more sustainable method: Bluesint PA12.
Bluesint uses the same material powder as our laser-sintered PA12. Instead of tossing the excess used powder, we can now use it to fill our specially designed SLS machines and print parts with impressive properties.
Before this unique process was made possible by our team, the major challenge keeping manufacturers from using machines with only reused powder was the lack of quality in the resulting part.
“Previously, builds using 100% reused powder created parts that had an ‘orange peel’— low surface quality that resulted in a wavy texture,” explains Tom Craeghs, Research Manager at Materialise. “In the years that we worked on this research, we had to find the exact order of steps and parameters that would prevent ‘orange peel’.”
The magic formula was a dual laser system, powered by Materialise software.
“We’ve created a laser sintering process that empowers our customers to make sustainable choices.” – Tom Craeghs, Research Manager, Materialise
“Because SLS machines are open systems, our team was able to fine-tune the parameters and, through much trial and error, finally develop the intelligent scanning strategy that builds a great material consisting of only reused powder,” says Tom. “Thanks to our team’s unparalleled expertise, our Build Processor to set these parameters, and the Materialise Control Platform to steer the process, we’ve created a laser sintering process that empowers our customers to make sustainable choices.”
Now, we’re able to build an eco-conscious version of our PA12 that offers the same mechanical properties. When you compare the two materials, stiffness, strength, long-term stability, and chemical-resistance are the same — the only difference is in surface quality. Bluesint PA12 has a slightly rougher surface quality, so it is a great fit for functional prototypes. And since prototypes have the sole purpose of validating designs, Bluesint is a wonderful opportunity to make prototyping more sustainable.
Once we finalize the validation of Bluesint, our team’s next steps are validating sustainably manufactured versions of our other SLS materials.
Enjoy our last month of anniversary savings! Get 10% off every Polyamide (SLS), Alumide, and Polypropylene order with code 30Y_SLS at checkout. Upload your model to save.
Recommended Articles
No related posts.