How It Works
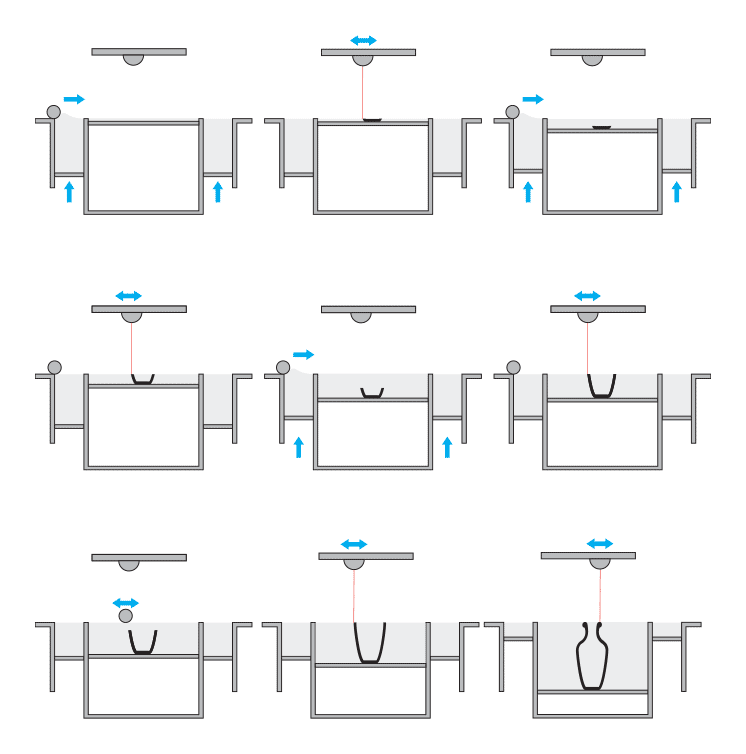
Starting from a 3D model, a model is built by cutting it into thin layers via specialized software. The model is then printed layer by layer by a laser that draws thin lines in the powder, which melts and bonds it together in order to form a thin layer of the model. After a layer is printed, a new layer of fresh powder is spread over the surface by a roller. The printer has a print chamber that is heated to just below the melting point of the powder; the laser beam adds the extra energy to melt the powder, forming a solid model. After a print job is finished, the result is a big block of heated powder with the printed models contained inside.
Materials
Polyamide
- Suitable for complex models, concept models, small series of models (several copies of a model), lamps, and functional models.
- Strong, somewhat flexible material that can take small impacts and resist some pressure while being bent
- Sandy, granular looking surface, but the material can be polished and/or dyed or finished with a velvet coating
- Slightly porous
- Allows the greatest freedom of design of all 3D printing techniques
Alumide
- A blend of gray aluminum powder and polyamide
- Suitable for complex models, concept models, small series of models (several copies of a model), lamps, and functional models.
- Strong, somewhat rigid material that can take small impacts and resist some pressure while being bent
- Sandy, granular looking surface, but the material can be dyed
- Slightly porous
- Allows the greatest freedom of design of all 3D printing techniques
Polypropylene
- Suitable for semi-rigid, functional prototypes with snap-fit or living hinges.
- Tough, fatigue resistant and durable translucent off-white
- Sandy, granular looking surface
- Some chemical resistance
- Allows the greatest freedom of design of all 3D printing techniques
Trivia
Did you know that?
- Laser sintering was developed and patented in the 1980s at the University of Texas at Austin, under sponsorship of DARPA, by mechanical engineering Professor Joe Beaman with student Carl Deckard and with guidance in laser technology and materials by Professor Dave Bourell. You can read the whole background story on www.me.utexas.edu.
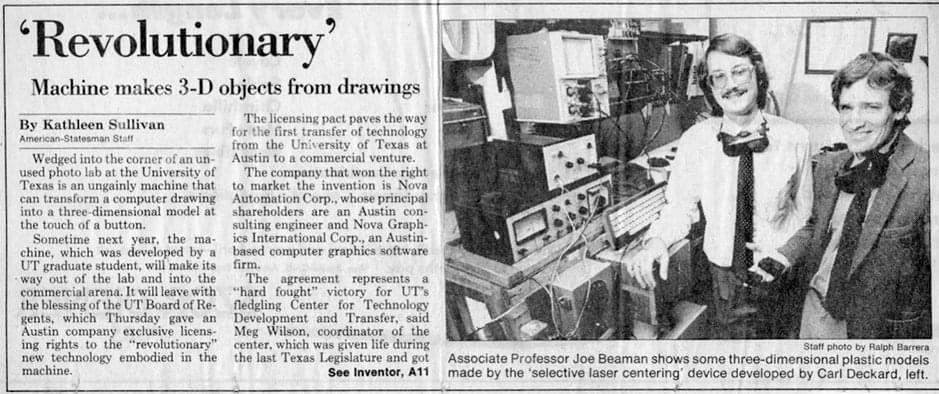
- Deckard and Beaman were involved in the founding of one of the first 3D printing startups, Desk Top Manufacturing (DTM) Corp., in 1989.
- The SinterStation 2000, the first commercial product, was originally designed by DTM Corporation in 1992 and marketed in 1993.
- Materialise has been using this technology since 1999.