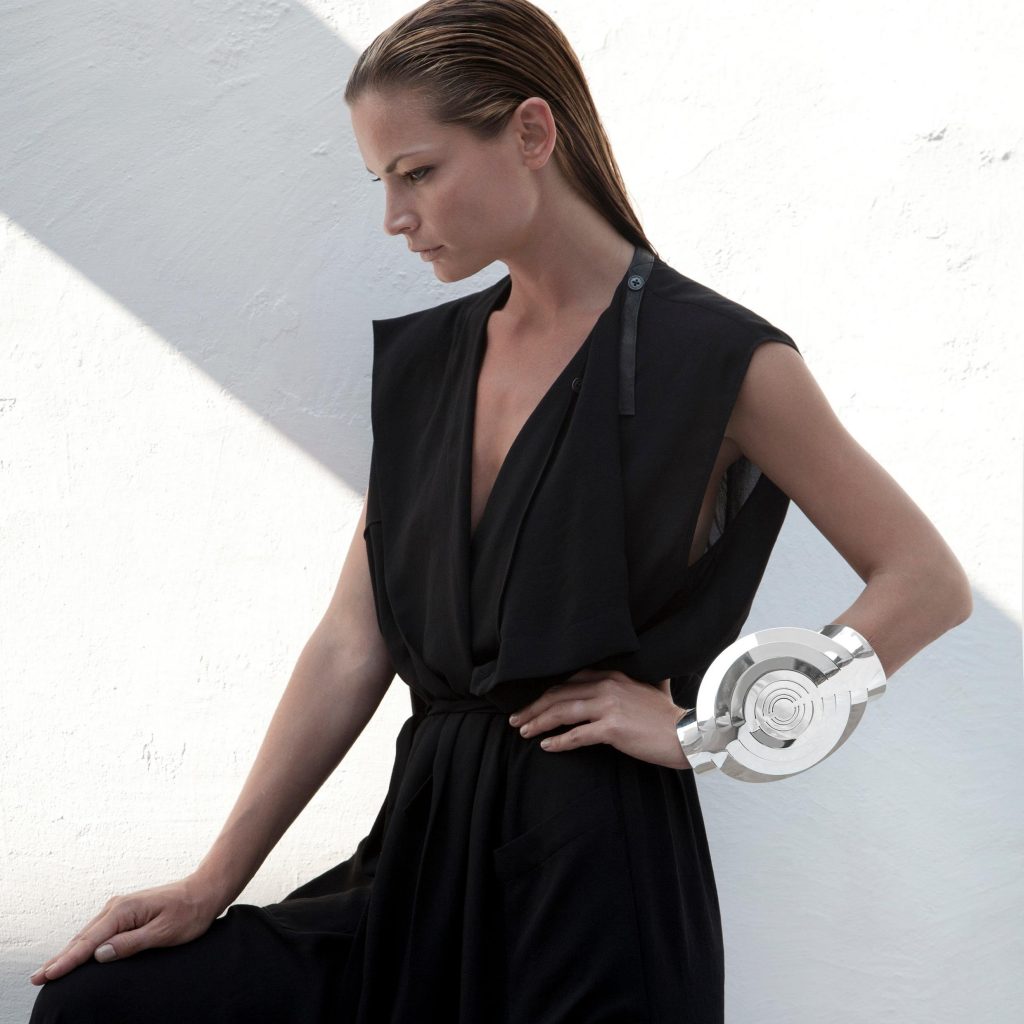
Using 3D Printing to Create Artisan Jewelry
London-based jewelry brand Maria Piana strives to create a new form of abstract jewelry, using intricate industrial processes and artisan experimental techniques. 3D modeling has become the backbone of creating their design aesthetic and bringing their unique visions to life, elevating their collections in ways not possible before. One of the co-designers at Maria Piana, Constantino Papaconstantinou, walked us through the brand’s creative and technical processes to design and create 3D printed jewelry.
When Constantino Papaconstantinou’s and jewelry designer Maria Piana’s paths crossed for the first time, it was a charmed chance meeting. As a design team, their pieces evoke a sense of sophistication and luxury, with detailed and unique sculpturing made possible by 3D design.
3D-printed ring by Maria PianaPrior to joining forces, both had been working in jewelry for quite some time. Constantino has been in the industry for more than 20 years, working with international retail brands and then starting his own jewelry design company and lab. Maria Piana began her career as a dentist before pursuing her passion for jewelry and starting her namesake London-based brand. When they met, she had been working on her second collection and together Constantino and Maria expanded the Maria Piana brand to elevate the pieces from the statement line to include more wearable pieces.
The brand’s designs have been featured in Vogue and on other international magazine covers, and worn by celebrities such as Beyoncé and Lady Gaga.
Elevating the collection with 3D design
Constantino saw the potential of using 3D design to create jewelry back in 2003 when he first started experimenting with 3D software. 3D modeling software to design the jewelry has made it possible to visualize certain pieces and aspects of the jewelry in ways that were not possible before.
“Ever since I was a kid, I have been drawing and designing, from copying maps to sketching floor plans,” he tells us. “When I realized I could design and manufacture the types of pieces I was thinking of by using 3D software, I was fascinated and started learning Rhino.”
This has allowed Constantino to design and print more complex pieces.
“3D design gives you the opportunity to see things before they are constructed or manufactured, make any changes on paper, cut trial and error procedures, and speed up processes while being confident about the final result,” Constantino explains.
Maria Piana’s first collection consisted of waterjet-cut pieces, while the second collection took that next step forward and added a third dimension to the wearable line, to experiment with more complex and playful shapes and designs.
Taking a leap of faith with i.materialise
“I have 3D printers, casting machines, and furnaces in my own lab, but they are oriented towards custom gold jewelry. I did some online research I found i.materialise and their parent company Materialise, and because I trusted the results I saw in their portfolios, I proposed to Maria to take a shot with our first 3D printed pieces,” he says.
They have been using the i.materialise platform ever since.
“The quality and polishing of i.materialise is excellent, and overall I must say that it’s great value for money and it has saved me a lot of time trying to produce these large and complex pieces myself,” he says. He is able to simply upload the design to the i.materialise website, wait for the order to arrive and then add small final touches where needed (such as earring clasps).
As a dual team of collaborative designers with a passion for exploring new ways of designs, working with i.materialise and using 3D printing has been the ideal creative scenario. From a business standpoint, using 3D printing is also more economical, since the brand are looking to drop small collections of complex designs in brass or silver, and in small to medium quantities where economies of scale cannot be applied. To build the design, they use lost-wax casting as the technology which captures all the intricate and precise details of the pieces, making it ideal for 3D printed jewelry.
From a paper concept to a printed reality
Maria and Constantino start designing their collections using a mood board, with a selection of around 20 pieces per collection. Constantino then begins designing the 3D models. This is mostly done using Rhino, occasionally using other software to add some texture where necessary.
“I use a completely stripped-down version of Rhino with no add-ons or libraries because I like using parts designed by myself and skip the ready-made components in libraries,” he says of his work process. “This definitely adds to the identity of the design, makes it more difficult to copy, and in the end, makes you a more skilled 3D designer since you have to figure out custom solutions instead of resorting to cookie-cutter ones.”
Designs are then printed in brass to be showcased in exhibitions (Premiere Classe in Paris Fashion Week, during London Fashion Week, HOMI Milano) and then reprinted in brass or silver depending on orders. The finish the brand opts for brass is usually gold plating on a highly polished surface.
However, designing intricate pieces of jewelry isn’t without its challenges, Constantino explains.
“Sometimes we would like to add more information to the design, to make it more complex, to give it more layers, so to speak,” he tells us. “The change in mindset is the most important and realistic approach that they have to use when they are designing the pieces in 3D, whereas on paper, they can still be dreaming.”
“After all, when you design in 3D software, you are not only designing but you are simultaneously modeling,” he explained. “This means you are in a way constructing, so there must be a sweet spot between aesthetics and the ability to produce the actual design, a spot where the idea, purified by the filter of production methods we have in mind, becomes the final product design.”
Ready to add new dimensions to your own art or design projects? Simply upload your 3D model to our online 3D printing service and choose from lots of high-quality materials, colors, and finishes.
We love seeing what our community gets up to. Tag us on social media with #imaterialise for a chance to get featured!
Recommended Articles
No related posts.