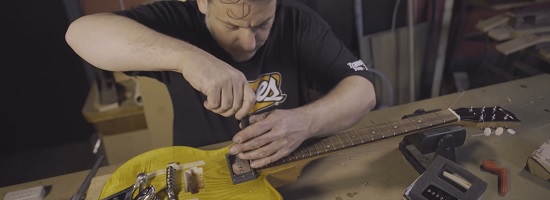
Designer Portrait: Master Luthier Hilko Nackaerts Enhances Guitars With 3D Printing
Luthier Hilko Nackaerts builds hand-crafted guitars that take the sound of a string to perfection. By combining traditional woodwork techniques with the cutting-edge technology of 3D printing, Hilko manages to create truly unique musical instruments. We met up with this talented designer to learn more about the passion that drives him and to listen to the sound of his 3D-enhanced guitars.
For more than a decade Hilko has been building guitars for a variety of internationally renowned artists including Roger Daltrey (The Who), Charlie Burchill (Simple Minds), Nile Rodgers (Chic), Ruben Block (Triggerfinger), Sarah and Gert Bettens (K’s Choice), Chris Rea, and many more.
Every guitar he makes is uniquely handcrafted. This way, Hilko breaks free from standardization and mass production and gives his guitars their true soul and sound. With the rise of 3D printing, Hilko saw an opportunity to enhance his designs by incorporating 3D printed parts:
“The value of 3D printing parts for my guitars lies in the little extra, the real customized personal touch I can give to an instrument. I like the mix of craftsmanship and technology, to blend that together in a final product.”
So which specific parts of the instrument are printed? Well, this depends on each guitar: “I have already used i.materialise to print my headstock logos, custom-made control knobs, pickup rings, or replicas of hard-to-find vintage guitar parts,” Hilko told us. Some of these designs include the logo of his brand, Hilko Guitars, which was 3D printed in Chrome-Plated Brass:
Another great example of his upgrades is the series of customized pickup covers below. A pickup device is a transducer that captures mechanical vibrations from guitars… and a 3D printed cover in Alumide sure gives them a great look!
Hilko designs the 3D models himself in 3D modeling software Rhino. It was a change for the master luthier to switch from pen and paper to a computer screen, but in the end, the advantages of 3D modeling prevailed: “I design everything in Rhino in 3D, which makes the process a lot easier because you are ‘inside the guitar.’ I used to be a pen and paper man, but when the technology became affordable, it helped me a lot to visualize everything before making it.”
Ironically, the speed of 3D printing (once known commonly as rapid prototyping) is not Hilko’s most appreciated advantage of the technology. It’s all about the quality: “New technologies don’t make guitar building particularly faster, but the results are simply much better. And our clients are thrilled with the results. Ruben Block from Triggerfinger was very pleased with the custom-made sterling silver headstock logo for his Hollowbody HC guitar.”
If you want to learn more about Hilko, take a look at his Facebook page. Keep an eye out for future blogs highlighting how other creatives enhance their products with 3D printing or unleash your own creativity by uploading your model today.
Recommended Articles
No related posts.