Entgegen der allgemeinen Auffassung gibt es keine Einheitslösung beim 3D-Druck. Die verschiedenen 3D-Druck Technologien lassen sich in 2 Gruppen aufteilen: Direkter und indirekter 3D-Druck. Der Hauptunterschied zwischen den 2 Gruppen besteht darin, dass das 3D-Modell entweder "direkt" mittels 3D-Druck hergestellt wird oder 3D-Druck nur "indirekt" als Teilschritt des Herstellungsprozesses verwendet wird. Lasersintern, eine der meist verbreiteten 3D-Druck Technologien, ist ein direktes 3D-Druck Verfahren.
Wie es funktioniert
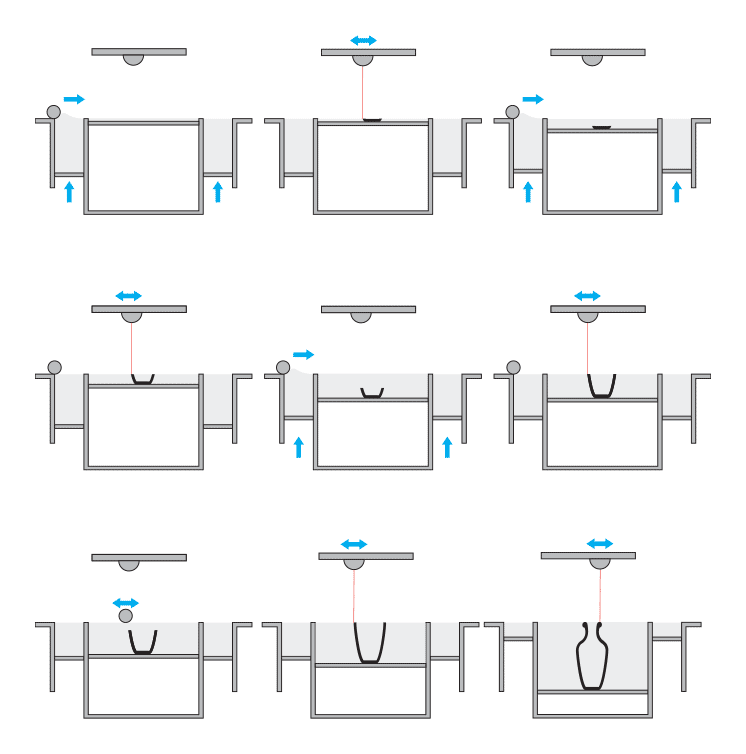
Materialien
Polyamid
- Geeignet für komplexe Modelle, Konzeptmodelle, Kleinserien, Lampen und Funktionsmodelle
- Stabiles, leicht flexibles Material, das leichteren Stößen und Druckbelastungen bei Verbiegung standhält
- Körnige, sandähnliche Oberfläche, die poliert und/oder gefärbt oder mit einer samtweichen Beschichtung versehen werden kann
- Leicht porös
- Erlaubt die größte Gestaltungsfreiheit aller 3D-Druck Verfahren.
Alumide
- Eine Mischung aus Aluminiumpulver und Polyamid
- Geeignet für komplexe Modelle, Konzeptmodelle, Kleinserien, Lampen und Funktionsmodelle
- Stabiles, strarres Material, das leichteren Stößen und Druckbelastungen bei Verbiegung standhält
- Körnige, sandähnliche Oberfläche die gefärbt werden kann.
- Leicht porös
- Erlaubt die größte Gestaltungsfreiheit aller 3D-Druck Verfahren.
Polypropylene
- Suitable for semi-rigid, functional prototypes with snap-fit or living hinges.
- Tough, fatigue resistant and durable translucent off-white
- Sandy, granular looking surface
- Some chemical resistance
- Allows the greatest freedom of design of all 3D printing techniques
Wissenswertes
Schon gewusst?
- Lasersintern wurde in den 1980ern an der University of Texas in Austin von Joe Beaman, Professor für Maschinenbau, und seinem Studenten Carl Deckard, mit wissenschaftlicher Unterstützung in den Bereichen Lasertechnologie und Materialien durch Professor Dave Bourell, entwickelt und patentiert. Gefördert wurde das Projekt durch DARPA. Sie können die vollständige Entstehungsgeschichte auf www.me.utexas.edu nachlesen.
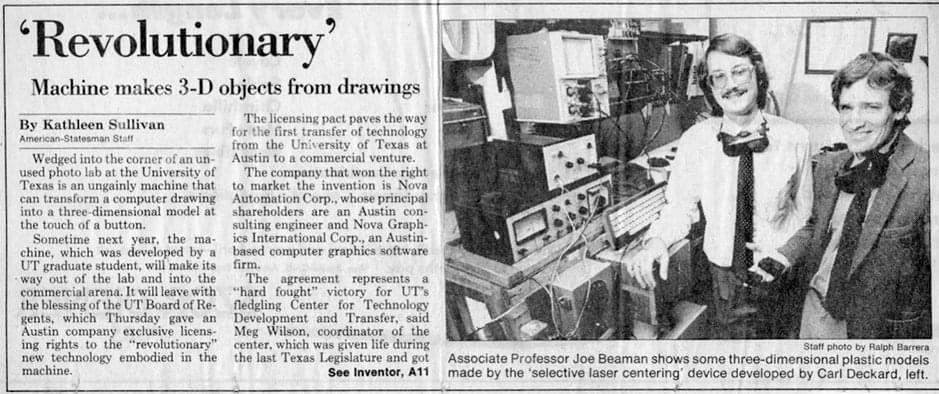
- Deckard und Beaman waren an der Gründung eines der ersten 3D-Druck Startups, Desk Top Manufacturing (DTM) Corp., im Jahre 1989 beteiligt.
- Die SinterStation 2000, das erste kommerzielle Produkt, wurde ursprünglich durch die DTM Corporation im Jahre 1992 entwickelt und 1993 auf den Markt gebracht
- Materialise verwendet dieses Verfahren seit 1999