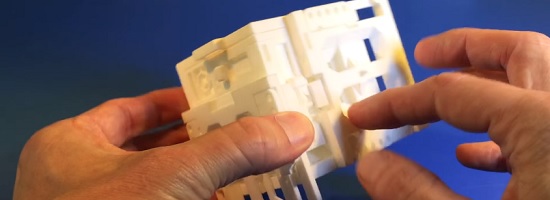
You Won’t Believe This Cube Was 3D Printed in One Piece
Meet Kurt Plagge, designer of one of the craziest (and smartest) designs we’ve seen lately. His small 3D-printed cubes are from a world of their own and were printed in one single piece. That’s right — no glue, no screws, and no manually attached parts. Thanks to laser sintering in Polyamide and his extreme 3D modeling skills, Kurt has managed to create a 3D-printed object unlike any other.
The Articulated Cube 5
Kurt uses Polyamide as a 3D printing material for his designs. Models in Polyamide are constructed from a very fine, white, granular powder that is sintered together by a 3D printer. This technology is referred to as laser sintering. It allows for moving and interlocking parts — that’s how Kurt was able to print his outstanding designs all in one piece.
After taking a look at Kurt’s newest cube, we just had to meet the designer and learn more about him and his designs!
Hi Kurt, please tell us about yourself.
I’ve always lived in Iowa (USA). I graduated from Iowa State University with a degree in architecture, then did some graduate work in graphic design, specializing in computer graphics and 3D modeling.
I’ve had numerous jobs throughout my career as a draftsman, using traditional manual techniques. As an architecture student, I became familiar with architectural model building and started using the same tools and materials to build whatever it was I wanted to. Some of the results have been quite complex with many moving parts and I utilized materials such as cardboard, floor tiles, automotive gasket material, polished stones, and rubber sheeting.
For a living, I currently work in IT project management and security.
And what brought you to the world of 3D printing and 3D modeling?
When I became aware of 3D printing, I was intrigued. I had used SketchUp a few times in the past so thought I’d try to make something I could send to a 3D printer. I found i.materialise, and that’s what’s directed me down this path. I like SketchUp because it’s about as close as I can get to manual drafting, but in three dimensions. My background in drafting, computer graphics, and modeling, along with my experiences with making articulated objects out of “traditional” materials has led me to the creation of this, and previous, articulated cubes.
It astounds me that I can use a program downloaded for free from the internet, create something purely out of my imagination, send it off to a 3D printer, hold it in my hands, and it’s EXACTLY what I imagined and worked on so long on, down to every last detail. That pushes me to imagine more complicated, crazier objects that stretch my abilities and the capabilities of laser sintering.
The Articulated Cube 4
How did you come up with the idea for this cube and honestly… how did you design it in SketchUp?
I like the cube format for several reasons. They provide the maximum volume for the minimum printing price. I’ve made them modular (50 mm, 75 mm, 100 mm) so they stack together neatly. And once I decide on a size, they provide a constraint so I can focus on the details and not concern myself with the infinite other shape options. I find I tend to integrate peace signs, UFOs, and aliens in my designs. I like to insert a little humor to help me take this less seriously.
All of the cubes I’ve done have been printed already fully assembled and in the closed position. The most challenging aspects of using laser sintering for these types of designs are maintaining appropriate gaps between moving parts while maintaining an object that’s as tight as possible and having a plan to deal with the removal of the trapped powder between the moving parts. It typically takes me several hours to get all the parts moving freely after they come back from the printer.
I probably spend anywhere from 40 – 120 hours completing a design. This is my hobby and my pastime so the amount of time I spend doing this is inconsequential to me.
The Articulated Cube 2 was 3D printed in Alumide
You can see all of Kurt’s designs on his YouTube channel. If you want to learn more about the material and technology he used, take a look at our Polyamide page. If you have a 3D model that you want to send to our industrial 3D printers, simply upload it here for an instant price quote.
Recommended Articles
No related posts.