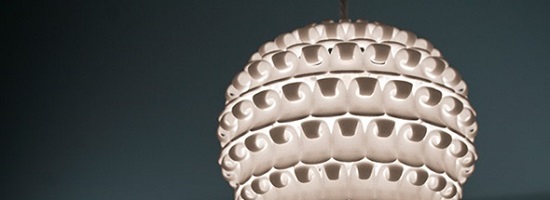
Life As a Professional 3D Designer: Meet 3D Artist Pekka Salokannel
Pekka Salokannel lives the 3D printed dream. The industrial designer from Helsinki creates 3D printed products, gives 3D modeling workshops, has worked for Tinkercad, Makerbot, and Mozilla, and launched his own 3D design company in 2013. Pekka is currently developing 3D printed eyewear, jewelry, and fashion items – reason enough for us to talk with him about his future projects, the ambition of professional 3D modelers, and the added value of 3D printed products.
Hi Pekka, please tell us a bit about yourself.
I’m Pekka, an entrepreneur balancing between my personal company Fabrigate and Kokosom where I’m one of the three founders. Kokosom is focusing on customized eyewear frames that are 3D printed and sold online. It’s a very interesting traditional industry that needs to be disrupted and we’re in the forefront to make the change. Fabrigate focuses on 3D printing and design consultation: jewelry design, product design, lectures, workshops, etc.
Portrait photo of Pekka Salokannel
Business card case by Pekka Salokannel
SOS eyewear by Pekka Salokannel. Photo by Stephanie Schweiger.
When and why did you start with 3D modeling?
It was probably around 2005 when I first saw a 3D printed product online, I believe it was one of Janne Kyttänen’s designs. He has been one of my sources of inspiration. It got me so excited and I started to think what I could do with 3D printing. When 3D printing services started to appear around 2009, I created a pair of earrings and ordered them on their website. They cost me 5 euros plus delivery costs. So, for 15 euros, I had my first real 3D print – not a prototype but a real end-product.
What value does 3D printing add to your design?
The forms are one value that sometimes aren’t possible to achieve with other techniques. Surface quality is also an issue sometimes, in a positive way. The biggest value is definitely just the possibility to even create a physical design. Most probably I wouldn’t have done any of my 3D printed designs with traditional techniques, so that’s what I mean by “even creating a physical design”. Without 3D printing, I probably would create totally different designs than now and a lot more concepts without physical products as an end-result.
How do you help others to get 3D models?
I’ve created a lot of designs in Tinkercad while working there and those are all free to use under a creative commons license. I’ve got almost 1,000 designs on my profile there but naturally most of them are just copies of others’ designs because that’s how Tinkercad works. Also, I’ve uploaded a couple designs to Thingiverse and other platforms to download or stream 3D models. I also lecture and hold workshops that are a good way to spread knowledge about 3D printing in general. Seeking 3D models is part of the lectures and workshops content, naturally. Additionally, I help people creating 3D files via i.materialise’s professional 3D modeling service.
Saw wrench by Pekka Salokannel
Raspberry Pi case by Pekka Salokannel
What’s your ambition as a 3D designer?
Creating new designs is definitely one thing, but if I think about it, what I really would like to achieve is to once create a big hit. Just like what most musicians are looking for: a product or collection that would really sell well. Many designers usually dream about a design that sells itself. Of course we know that almost never happens. But I’d love to create a successful product that liberates my time to create more conceptual design, help others and travel more. To say it in short: “Design time”.
What is your typical workflow on a new 3D printing project?
I’ve got different inspiration boards that I collect and update weekly. I do sketching, but sometimes forms get so complex that it’s simply easier to create directly in 3D. Sketching is usually better when creating and visualizing masses, overall shapes and also when thinking about details. But putting these together is almost always better to on a computer. When I start to be happy about the design, I 3D print it.
Where do you get your inspiration from?
It depends on the work. For jewelry, nature is typically a good starting point. For more geometrical designs, I check what others have done and try my best to make it a little bit better than what I’ve seen. As Picasso said: “Good artists copy, great artists steal.”
Cresco lamp by Pekka Salokannel. Photo by FOC.
Park necklace by Pekka Salokannel. Photo by FOC.
If you need help in getting a printable 3D file, you can contact Pekka via our 3D modeling service. Would you like to offer your design skills as well and make some money? Then create your professional designer profile on our 3D modeling service here for free. Do you want to print your design in HD quality? Simply upload it here and let us take care of the rest!
Recommended Articles
No related posts.