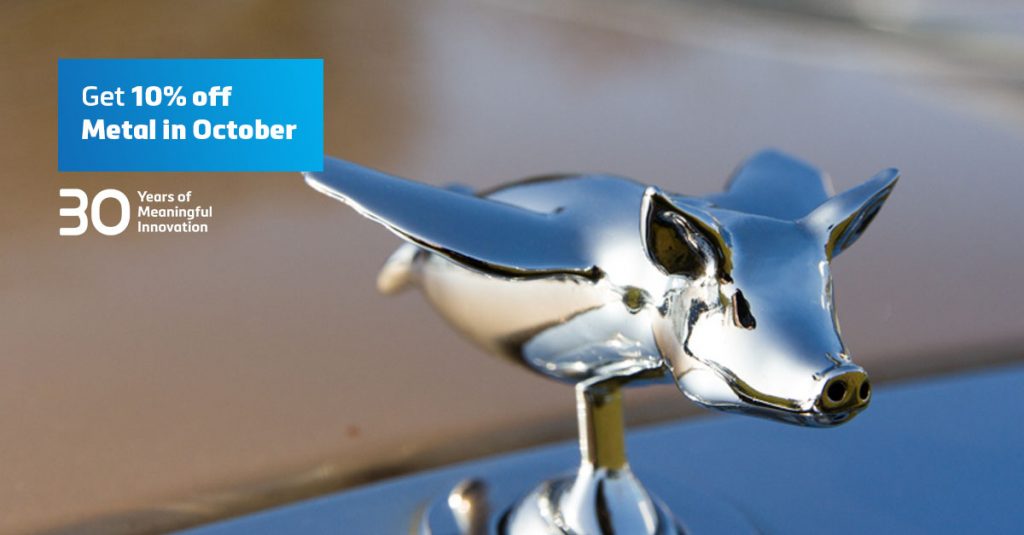
30 Years of Innovation: Bringing 3D Printing’s Benefits to Metal
We’ve passed the halfway point of our 30th-anniversary blog series, and for October, we’re looking into Metal 3D Printing. Read on to discover how our parent company Materialise utilizes Metal 3D Printing to combine AM’s advantages with tried-and-tested materials and how our team in Bremen, Germany is working to further develop the technology.
3D printing for plastics was the blueprint for AM innovators to create Metal 3D Printing processes. Once the laser sintering technology was patented, users began to experiment with applying the process to various metals as well. After a significant industry-wide research phase to improve the technology over the years, it became a reliable, high-quality option by the mid-2010s. At this point, Materialise brought Metal AM into our manufacturing portfolio to not only provide the printing service to our customers but to also use our AM expertise to further improve the technology.
The appeal of Metal AM was clear. Just like for plastics, companies now had to opportunity to receive parts faster than ever before, but now with robust materials. 3D printing doesn’t require the time-consuming creation of molds or production lines like traditional technologies — with a digital file in hand, almost any design can be printed within approximately ten working days. However, we recognized that more often than not, the orders Materialise received didn’t benefit from all of the technology’s advantages. With our know-how and design expertise, there was untapped potential that we could help our customers achieve —design freedom, cost reductions, and risk mitigation, for example.
So with Metal 3D Printing in our portfolio, we placed a focus on helping our customers leverage all of its benefits. And today, we continue to innovate to drive the technology and our metal services forward. Our team is working to see that Metal 3D Printing is not just a quicker alternative to manufacturing metals, but the preferred method.
The one-stop-shop for Metal 3D Printing
To become true specialists in Metal AM, we decided to expand our services into a location where we could both meet the demands of our orders and be near our customers and other leaders in the manufacturing world. That is why we opened a facility dedicated to Metal 3D Printing in Bremen, Germany in 2016. In this way, we could continuously learn about industries such as aerospace, automotive, industrial automation, and eyewear to advance our services.
Once the facility was in place, we could provide a service that assisted customers in using Metal AM to its full potential throughout the entire production process, from design to finish. “We offer a service that assists customers during each step of Metal 3D Printing,” shares Ingo Uckelmann, Technical Manager of Metal 3D Printing. “Our design and engineering, certified manufacturing, and post-machining teams are all extremely knowledgeable about how best to use the technology and ensure that our customers get the most out of it.”
Let’s demonstrate this idea with our design and engineering team’s work on optimizing the design of a metal suction gripper. The team worked closely with the customer to completely redesign their production part using Design for AM principles. Because of these changes, the brand-new part was 94% lighter, 50% cheaper, and more performant.
The original part (above) was not designed for AM, meaning it was much heavier and more costly than necessary.
The team also began initiatives to improve the quality and consistency of the technology — a mission that continues to remain a focus. To do so, the team began by ensuring consistent alloys via internal testing and aligning our alloy standards to that of our proven plastics offerings. For any metal prints i.materialise customers can choose between Aluminum, High-Detail Stainless Steel, Steel, and Titanium.
But these aren’t the only metals you can get on i.materialise — we also offer 5 precious metal options: Brass, Bronze, Copper, Gold, and Silver. Unlike our metal options, we use lost-wax printing and casting to manufacture these materials. With this printing process, which is a type of Stereolithography, customers can leverage 3D printing’s freedom of design with these stunning material options.
Gold is available as 14k or 18k solid gold in three different colors: yellow gold, red gold, and white gold.
Taking Metal AM to the next level
At Materialise, we’re constantly aiming higher to improve our technologies and make the advantages of 3D printing more accessible. This mission is no different with Metal AM. We want every customer to experience lighter parts, cost-effectiveness, and freedom of design combined with the durability of metal materials. Then, Metal 3D Printing will surely be everyone’s first choice for manufacturing, not just the option they turn to when they need a quicker alternative. This is why we’re installing the new Metal Competence Center at our Bremen facilities in early 2021.
“We’re developing the technologies of tomorrow.” – Ingo Uckelmann, Technical Manager of Metal 3D Printing
This center was created to bring together our experts in both AM software and production to advance Metal 3D Printing while supporting a sustainable future. Here, the team can face any economical or ecological challenge head-on and build solutions with Metal 3D Printing’s capabilities to overcome it. They uniquely combine expertise from the production floor with know-how from decades of AM software development to further increase the technology’s reliability and consistency.
Thanks to this collaboration, the Metal Competence Center production can be the first to work with the latest, most innovative software from our team, and the software developers can enhance software with direct feedback from production. This rapid feedback and development cycle enables the team to quickly and continuously improve their services to bring the best to customers.
Our specialized software, such as e-Stage for Metal, enhances the reliability and quality of 3D printing.
“At our Metal Competence Center in Bremen, we’re developing the technologies of tomorrow,” explains Ingo. “By improving Metal AM to make it easier, more accessible, and more affordable, we will ensure that it’s a viable technology that companies will turn to first for their metal parts.”
As we’ve looked deeper into our own processes and fine-tuned Metal AM software and workflows, we’ve effectively automated many tasks, thus shortening lead times and lowering costs. Enhancing the technology through automation and design for Metal AM helps our customers reach the next level with their metal parts while keeping costs low. For series productions, we work alongside customers to enable customization and improved parts with the power of Metal 3D Printing — all while meeting their time, financial, and quality expectations.
Let’s get started
Ready to print your own projects in Aluminum, High-Detail Stainless Steel, Steel, Titanium, Brass, Bronze, Copper, Gold or Silver? Get your parts quicker than ever by ordering online via i.materialise. Until October 31, we’re offering an extra 10% off all Metal and Precious Metal orders when you use the code 30Y_Metal at discount.
Recommended Articles
No related posts.