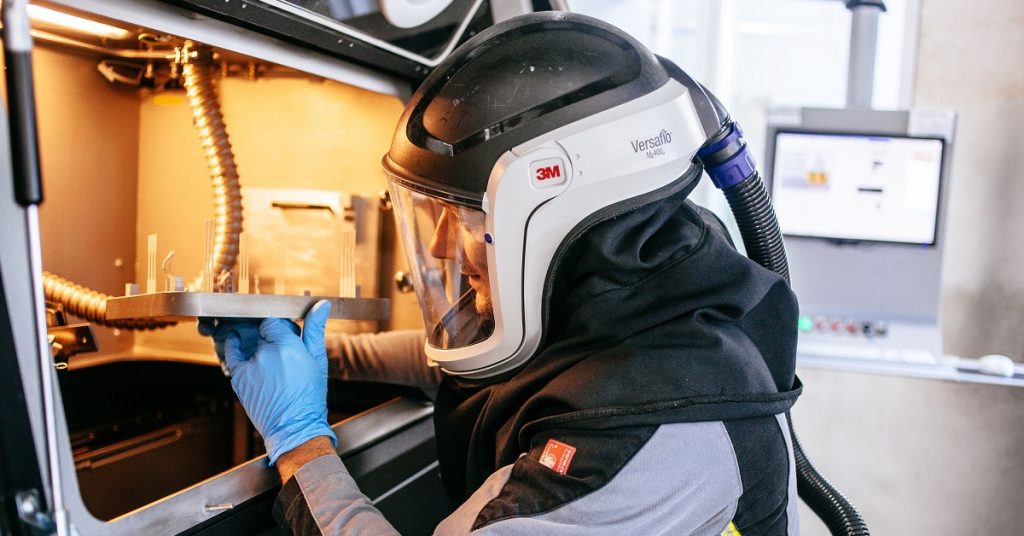
How Direct Metal Laser Sintering (DMLS) Really Works
Direct metal laser sintering is one of the most fascinating 3D printing techniques, as it allows you to print your own designs in metals such as Aluminum or Titanium. Today we will take a more detailed look at this technology and see how you can access it via our online service.
Direct Metal Laser Sintering
Direct Metal Laser Sintering – or DMLS for short – is a game changer when to comes to direct 3D printing of metals. This ultra high end 3D printing process is one of the world’s most advanced manufacturing technologies. But take a look for yourself:
The Base Material: Metal Powder
Unlike with most home printers, DMLS printers do not use filament. In fact, the 3D printed parts are constructed from very fine, granular Aluminum or Titanium powder. It is important to note that the powder used by 3D printers cannot be any kind of powder. Since it will be used for ultra-thin printing layers, the powder must be perfectly shaped in order to even out. Consider rocks and marbles; you could easily put rocks on top of each other to build a pyramid. However, building a pyramid with marbles would be way more difficult, as the perfectly shaped spheres would just even out and your pyramid wouldn’t stand a chance. Similar to the marbles, the Aluminum and Titanium powder needs to have the perfect shapes of spheres since each and every printing layer needs to have exactly the same height (and we’re talking about microns here).
Cheetah Bike Stem by Nils Faber. 3D printed in Aluminum.
Cufflinks with Ginko Leaf by Steve Koll. 3D printed in Titanium.
The Printing Process of DMLS Explained
To create your 3D print, a laser in the printer melts the powder together. So here’s how it works: A super-thin layer of Aluminum or Titanium powder is spread out by a roller. The print chamber of the 3D printer is then heated up. However, the powder does not melt yet since it has not reached its melting point. And now the magic happens: a laser touches those areas of the layer that are part of your design, raising the temperature of those areas just above the melting point, and voilà, your part is sintered (well, one layer of your part). The 3D printer will continue to spread out one layer of powder after another, and the laser will systematically touch the correct spots of each layer and sinter the object together.
Section view of the DMLS 3D printing process.
After the Printing: Cooldown & Finishing
Once the printing job is done, it is not possible to immediately grab the 3D prints – the printer and the metal parts still need to cool down. Once this period is over, your model is lifted from the powder bed. If your model needs support structures to keep the model structurally sound or to support it while the 3D printer builds it, they will be removed manually.
A metal model is taken out of a 3D printer at Materialise’s Metal 3D Printing factory.
How to Get a High-Quality DMLS Print in Titanium and Aluminum
To get the best prints in Titanium and Aluminum, check out our design guidelines. There you can see more of the technical specifications, such as wall thickness, accuracy, and typical use to make sure your print will come out exactly as you imagine.
At i.materialise we’re committed to letting you make the future. If you would like to print your design in Titanium, Aluminum, or one of our 100+ other materials and finishes, upload your 3D file here and see the price of your model within seconds.
Recommended Articles
No related posts.