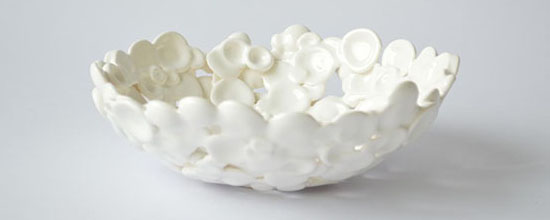
Ceramic “3D Crafts” by Alice Le Biez: A Delicate Fusion of 3D Printing and Traditional Craftsmanship
It will never match the warmth of a hand-made product: this is one of the myths about 3D Printing. But now with the introduction of “3D Crafts,” a set of 3D Printed ceramic bowls designed by French graduate student Alice Le Biez, that myth is about to be shattered for good. With a variety of 3D Printing materials that now go far beyond plastics, ancient craftsmanship and edgy technology can be beautifully blended to bring the emotion of a design to life.
1. Tell us a bit about yourself.
I come from a small town called Guérande, located in Brittany in the west of France. After receiving a Baccalaureate in 2006, I started learning traditional techniques to decorate pieces of furniture at the Ecole Boulle, Paris. Then I moved to Brussels to start my Bachelor in Industrial Design at the National School of La Cambre. I acquired practical skills to make an object in Paris, but in Brussels I learned more about the conception and the development of ideas. Graduating La Cambre in June 2013, I decided to continue my education with a Master’s in Product Design at the Manchester Metropolitan School of Art in the UK where I had the opportunity to develop my bowls in ceramics. These 3D Printed bowls – “3D Crafts” – were exhibited last month at the MA Show 2014 in my school.
2. How did you become interested in ceramics?
When I was studying at the ENSAV La Cambre in Brussels, I had the opportunity to develop a project in porcelain. I used the properties of this material to create a natural amplifier of sounds. For two months, I was working in a ceramics workshop where I could interact with others students and learnt more about their discipline.
3. When did you start using 3D Printing technology? Which tool or software do you use most?
I am working with Solidworks 2014, it’s a 3D software which allows me to build my ideas. I was interested in this new technology since the beginning but I only had the opportunity to use it at the Manchester Metropolitan School of Art during my Masters. I started first with an ABS 3D Printer before pursuing other materials such as acrylic, nylon and ceramics.
4. Why did you choose 3D Printing over other options (such as traditional casting)?
First, I chose to 3D Print in ceramics to save time. Normally, ceramic is a material which needs a lot of time and attention. The designer has to conceive the mould in plaster, let it dry, then he probably has to try several times to get a perfect result. Ceramics 3D Printing allowed me to create my bowl directly in the [exact] dimensions because the material didn’t shrink, and I was surprised how quickly it can be done when I received my final product in 10 days after ordering it at i.materialise.
Another reason is because I really wanted to explore this technique. My aim was to create an object which looks like a hand-made product. When I talk about 3D Printing in plastic with people around me, many believe it is a technology that will create more waste or unnecessary objects. But when I talk about crafts, hand-made objects, their perception changes. They give instantly more value to a hand-made product.
I really wanted to change their mind and show that designers and craftsmen can create valuable, emotional objects with 3D Printing.
5. You 3D Printed the bowls in several materials other than ceramics. What were the differences you’ve found in those materials?
Indeed, I made a set of three bowls in three different materials: acrylic, nylon and ceramics. I was interested in the 3D Printing process and how different materials [elicit] different perceptions from people.
I first printed a set in acrylic. The three bowls in acrylic are exactly what most people expect from a 3D Printed object. It looks cheap because it’s plastic and the colour is slightly yellow. When I asked people what they thought about it, they said that it looks cheap and it’s a disposable product. Definitely not a valuable object.
The second set was printed in nylon. The texture of the material is sandy, which gives a nice play between light and shadows. People found it more valuable because of the texture and the colour, which is really white.
The last set was 3D Printed in ceramic through i.materialise. People thought that it was a hand-made product because of the material. They were surprised to learn that we can print this kind of design in ceramics! Glazed ceramics looks more natural and hand-made compared to other materials, and it gives a lot of value to this set of bowls.
That was really interesting because, of the three sets, the ceramic one was the cheapest one to make.
6. Which material is your favourite to 3D Print in, and why?
I really enjoyed working with ceramics. Ceramic is a material that is associated with history and craftsmanship. The first ceramic pottery dates back to Greek history and the time of the Gauls and the Romans.
Normally designing in this material requires an ancient technique. Realizing ceramics through 3D Printing was challenging, but it also showed me a new direction to create something different. Ceramic is also a material that is associated with fragility, beauty, something that has value. All of these elements make it really interesting.
7. What are your tips and suggestions for creating 3D Printed ceramic art?
For people who want to create a 3D Printed ceramic art, I would suggest first to meet a ceramist to understand the material. I believe it’s essential to understand and know about the material, its limitations (thickness…). Knowing the material will give you the opportunity to expect the result and go further in the work.
8. Which part of your design process was the most complex or difficult?
The inability to see my product before it was 3D Printed was the most difficult part. Even when I develop my design on 3D software, it’s important for me to see, analyse, and touch the prototype in order to modify it. But at the same time it’s amazing to see that my idea directly 3D Printed and was made ready-to-use.
9. What advice would you give to new sculptors and 3D designers?
I would just say to 3D designers to continue to push the borders of creation and the limits of the machine. It’s amazing to discover new possibilities with 3D Printing.
If you’re motivated to 3D Print ceramic tableware just like Alice’s “3D Crafts,” here’s our helpful design guide. As she says, you’ll be surprised to see how quickly your idea can be turned into a seemingly hand-made ceramic object – we can have ceramic projects with thick and glossy glazing back to you in just 15–20 days. What would you “craft” with our bright, food-safe, and fast ceramics?
Recommended Articles
No related posts.