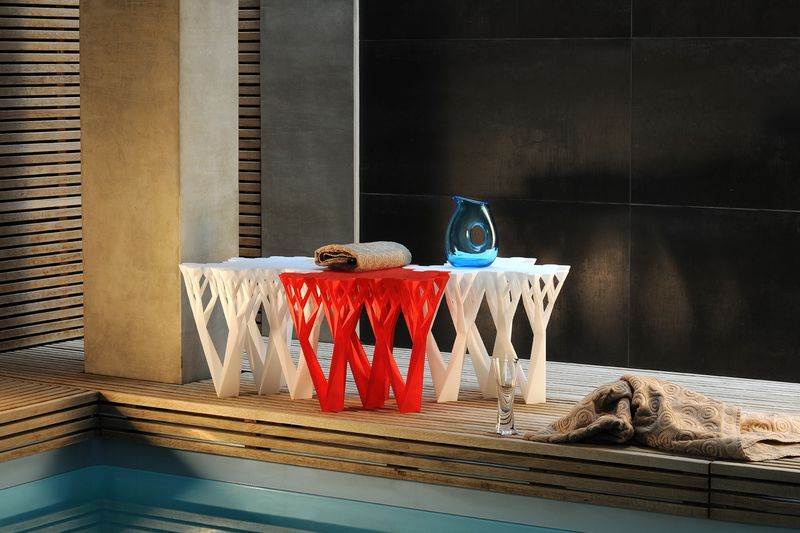
3D Printing Technologies: Fused Deposition Modeling
Contrary to popular belief, there’s not a one-size-fits-all approach to 3D printing. Although we offer 17 different materials and over 90 possible color and finish combinations, it often takes us several different technologies to get the job done. In general, 3D printing technologies can be split up into 2 groups: direct and indirect 3D printing. The main difference lies in the fact that the design is made from 3D printing (direct) or 3D printing was used in the process of creating your model (indirect). Let’s move on with the third part of this series with fused deposition modeling, probably the most adopted 3D printing technology around and an example of a direct 3D printing technique.
How It Works: Fused Deposition Modeling (FDM)
The Basic Principle
Fused Deposition Modeling is used to build your designs in ABS. The principle is simple. You can compare it with a hot glue gun into which you put sticks of glue. The glue is heated up until it melts and is then pushed through a fine nozzle in the front of the glue gun.
In a professional FDM printer, a long plastic wire is used in place of glue. It is fed by a spool to the nozzle where the material is liquefied and ‘drawn’ on the platform where it immediately hardens again. The nozzle moves to drop the material at the correct location, drawing your model line by line. When a layer is drawn, the platform lowers by one layer thickness so the printer can start with the next layer.
When your model contains overhanging sections, the printer needs to build supporting material. Since the material of the model cannot be deposited in the air, the support material prevents it from falling down. This support material is fed through another nozzle. Afterward, when the model is put into a bath with a special soap, the support material dissolves.
FDM Material
Nokia Lumia 820 case by Dries Vandecruys
- Suitable for full functional models (it has 80% of the strength of injected molded ABS)
- UV resistant
- Come closest to the material of real production models
- Layer thickness between 0.13 – 0.25 mm
FDM Printing Sizes
Trivia about 3D Printing with Fused Deposition Modeling
Did you know that?
- The technology was created in 1988 by S. Scott and Lisa Crump, the founders of Stratasys. Crump created the technology to build his daughter a toy frog using a glue gun and a mixture of polyethylene and candle wax.
- Fused Deposition Modeling was invented and patented in 1989 by S. Scott and Lisa Crump as a technology for 3D printing where material is extruded out of a nozzle and creates a 3D object layer by layer.
- The term Fused Deposition Modeling and its abbreviation to FDM are trademarked by Stratasys. The exactly equivalent term, fused filament fabrication (FFF), was coined by the members of the RepRap project to give a phrase that would be legally unconstrained in its use.
- In 2009, the patent for Fused Deposition Modeling expired and ignited the whole industry 3D printing industry.
- Materialise has been using this technology since 2003.
Can’t get enough of this exciting technology and its materials? Then dive into our elaborate material pages for a lot more information or get your FDM printed part by uploading it to our online 3D printing service page here.
Recommended Articles
No related posts.