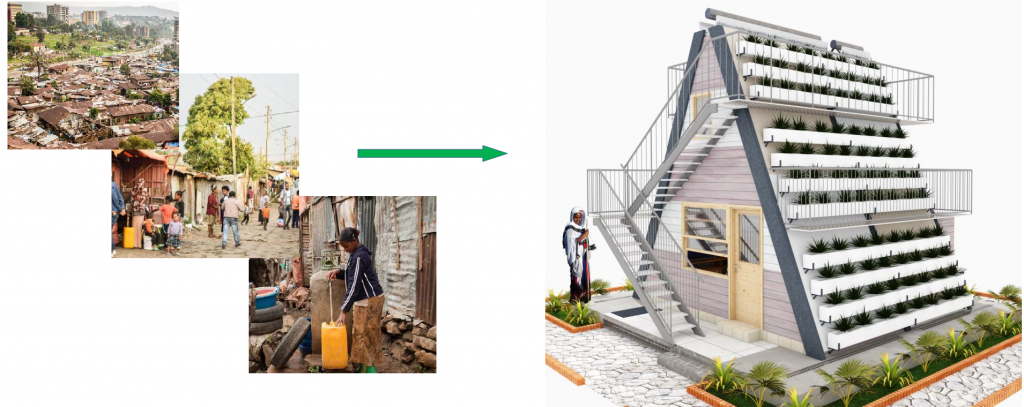
3D-Printed Molds For Special Concrete Pillars Brings Revolutionary Sustainable House One Step Closer
Sustainability, environmentalism, and climate change are subjects at the forefront of hearts and minds across the planet. Recent events, from forest fires and floods to record weather temperatures and shifting ecosystems, indicate that we must make a concerted effort to come up with sustainable solutions to global issues. One such problem is providing adequate shelter to urban slum families in sub-standard housing in Africa. What could help solve this crisis? The Tridealhouse project.
Tridealhouse — a triangular house that stimulates happy living, urban farming, and sustainable utilities to help tackle urban poverty — solves five slum household deprivations as defined by the UN-Habitat while providing food and micro jobs. To confront such wide-ranging issues, this ambitious project needed more than just theoretical knowledge, it also required specific materials and expertise. That’s why the Trideal team contacted our parent company, Materialise, to collaborate on making special, 3D-printed molds for their distinct concrete pillars — forming the bedrock of the design and bringing the project one step closer to fruition.
“Most of the world’s problems could be solved by integrating innovation with social/humanitarian entrepreneurship,” states Dr. Michel Loots, Founder and CEO of Tridealhouse. Working with UN agencies for the past 25 years and with an extensive background in medicine, economics, international relations, and entrepreneurship, Michel believes that free market principles can coexist with humanitarian entrepreneurship. And this was the inspiration behind the collaboration with Materialise.
Tridealhouse is a triangular house that stimulates happy living, urban farming, and sustainable utilities to help solve urban poverty.
Made from the same mold: entrepreneurs and innovation go hand in hand
Using his contacts in the group Ondernemers voor ondernemers (Entrepreneurs for entrepreneurs), Michel decided to reach out to Materialise to solve a particular challenge: how could his team create original side panels for the house — normally too complicated to make through traditional milling techniques — rapidly and at scale?
“Timing was of the essence, as Michel was flying out to Addis Ababa, Ethiopia, to discuss the project with key stakeholders,” recalls Gertjan Brienen, Sales Engineer at Materialise. After a quick consultation, both parties agreed that fused deposition modeling (FDM) was the technology of choice coupled with ABS material.
“For the 3D-printed molds, we opted for an FDM/ABS combination, as it’s sturdy, durable, and can withstand high temperatures. Another benefit is the accuracy in which we can use it to form and shape ambitious designs. It’s quick to print and was the most suitable candidate, especially for big parts such as this,” remarks Dieter Ferlin, Sales Engineer, Manufacturing Division at Materialise. After a few tweaks and some small modifications, the molds were ready, all within a few days. “Quick collaboration, communication, and timing; that was our goal. And providing our technical expertise to find a solution that works of course,” agreed Gertjan and Dieter.
“Tridealhouse is a perfect example of how 3D printing can make an impact environmentally and socially. This project also reaffirms our mission statement of utilizing technology to innovate product development. It allows us to apply our knowledge of AM to drive positive outcomes for society and enables our customers to design sustainable solutions. From small-scale designs printed by budding hobbyists to sustainably developed, triangular houses, AM is improving the lives of people every day,” — Gertjan Brienen, Sales Engineer at Materialise
Due to the composite panel’s unique design, the team had to create special, 3D-printed molds to house the concrete.
Michel and the Tridealhouse team were extremely impressed with Materialise’s expertise and the outcome. And the silicone molds used to form the composite, concrete panels exceeded their expectations, ready for the trip to Addis Addaba. The Tridealhouse concept was unanimously praised by the stakeholders in Ethiopia and is now in the advanced stage of development. The first, full-scale prototype of the house is scheduled for completion by the end of December leading into January.
Tridealhouse provides a truly sustainable solution for those affected by urban poverty
Made from concrete and steel, these houses will be resistant to droughts, floods, and earthquakes with an estimated lifespan of 80 years. Along with offering protection, these buildings are ecological with harvested and disinfected water, in-house sanitation, and powered by solar PV and thermal energy. Not to mention, the house is also self-financing, allowing the inhabitants to grow their own vegetables and look after micro-livestock (for consumption or reselling), making the occupants economically independent.
“There are five key stakeholders: governments, UN/ODA, universities/R&D institutions, impact investors, and the industry (thought leaders). It’s important that we have the support of the manufacturing industry, as this is the fountain of technological innovation which can make a big difference. Materialise is a prime example: we’re grateful for their proficiency, proactiveness, and rapid turnover,” praises Michel. “The house is designed for mass production — using locally sourced materials and manpower — which means that we must have the right components on-site,” said Michel. This is where 3D printing comes into its own, a technology that is ideal for filling in the gaps where traditional processes falter.
“Tridealhouse is a perfect example of how 3D printing can make an impact environmentally and socially. This project also reaffirms our mission statement of utilizing technology to innovate product development. It allows us to apply our knowledge of AM to drive positive outcomes for society and enables our customers to design sustainable solutions. From small-scale designs printed by budding hobbyists to sustainably developed, triangular houses, AM is improving the lives of people every day,” Gertjan concludes.
Ready to 3D print your own projects?
Recommended Articles
No related posts.