How It Works
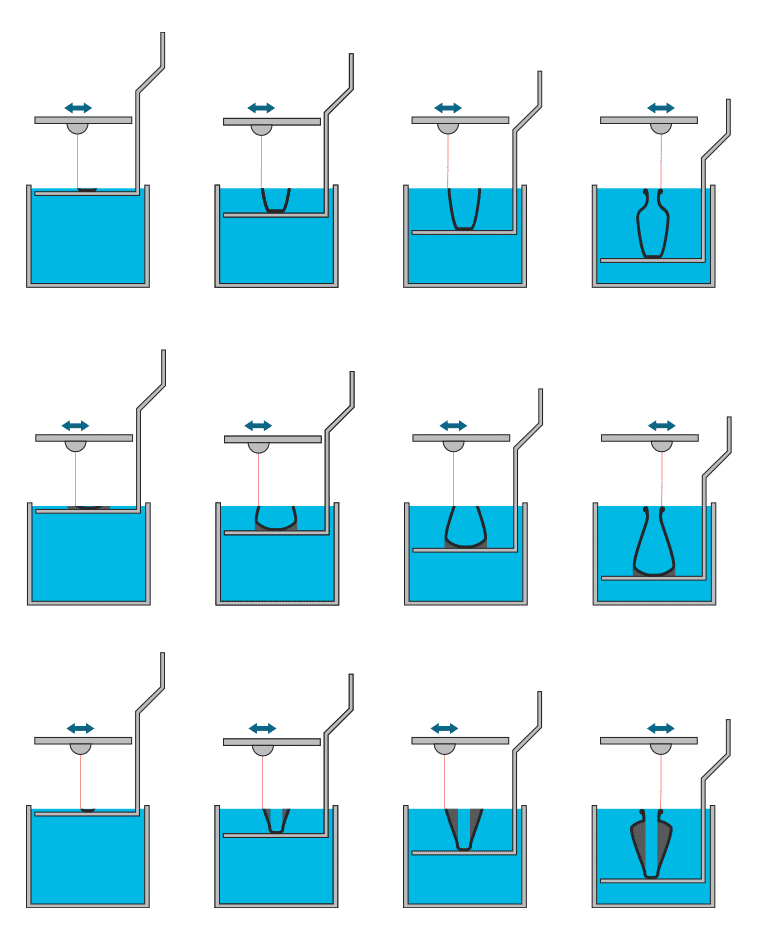
Starting from a 3D model, a model is built by cutting it into thin layers via specialized software. A support structure is created, where needed, in order to deal with overhangs and cavities.
The process takes place in a large tank and begins when a layer of liquid polymer is spread over a platform. This machine then uses a computer controlled laser to draw the first layer onto the surface of a liquid polymer, which hardens where struck by the laser. The model is then lowered and the next layer is then drawn directly on top of the previous one. This is repeated until the model is finished. In this way, layer by layer, an object is “drawn” in the liquid by the beam, with the layers being consolidated throughout the process.
When the object is complete, it is raised out of the tank via the supporting platform – much like a submarine rising to the surface of the water – with the excess liquid flowing away. The supports are removed manually after the model is taken from the machine.
Materials
Standard Resin
- Suitable for A-side visual models with limited functionality
- Smooth surface, much smoother in fact than almost all other 3D printing materials
- Easy to paint
- Limited freedom of design because of the necessary support structure
Gray Resin
- Suitable for A-side visual models with limited functionality
- Smooth surface, much smoother in fact than almost all other 3D printing materials
- Easy to paint
- Limited freedom of design because of the necessary support structure
Mammoth Resin
- Suitable for (large) visual models with limited functionality
- Smooth surface
- As its name suggests, the material is great for painting
- Limited freedom of design because of the necessary support structure
Transparent Resin
- Suitable for (large) models needing a good, smooth, quality surface with a transparent look
- Ideal for demo models, accurate models, and models with limited functionality
- The color of the material is transparent, but not 100% water clear
- Limited freedom of design because of the necessary support structure
Trivia
Did you know that?
- Stereolithography is derived from the Greek word stereo (solid body), litho (stone), and graphien (to write).
- Stereolithography is the oldest 3D Printing technology
- In November 1981, Hideo Kodama of the Nagoya Municipal Industrial Research Institute (Nagoya, Japan) published a paper titled ‘Automatic Method for Fabricating a Three-Dimensional Plastic Model with Photo Hardening’. Kodama describes three basic techniques he used to create plastic parts by solidifying thin, consecutive layers of photopolymer. It’s said that Kodama’s experiments were perhaps the first evidence of working additive manufacturing (AM) techniques in the world.
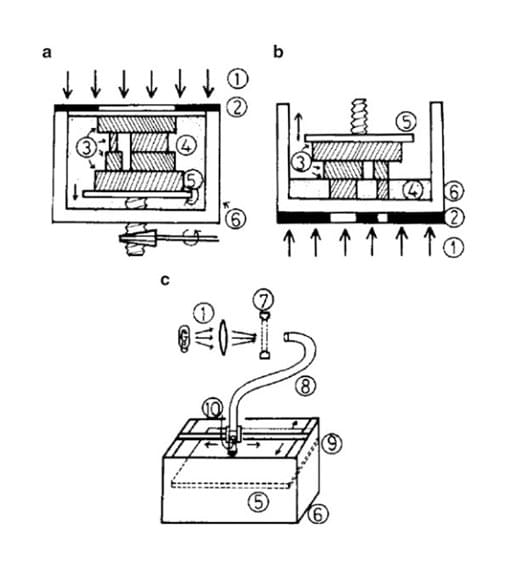
- On March 11, 1986, Charles (Chuck) W. Hull patented the method of stereolithography. He also coined the name in U.S. Patent 4,575,330, entitled “Apparatus for Production of Three-Dimensional Objects by Stereolithography”. Hull defined stereolithography as the method of making solid objects by successively laying down thin layers of ultraviolet curable material one layer at a time through the use of the apparatus.
- Materialise has been using this technology since 1990.
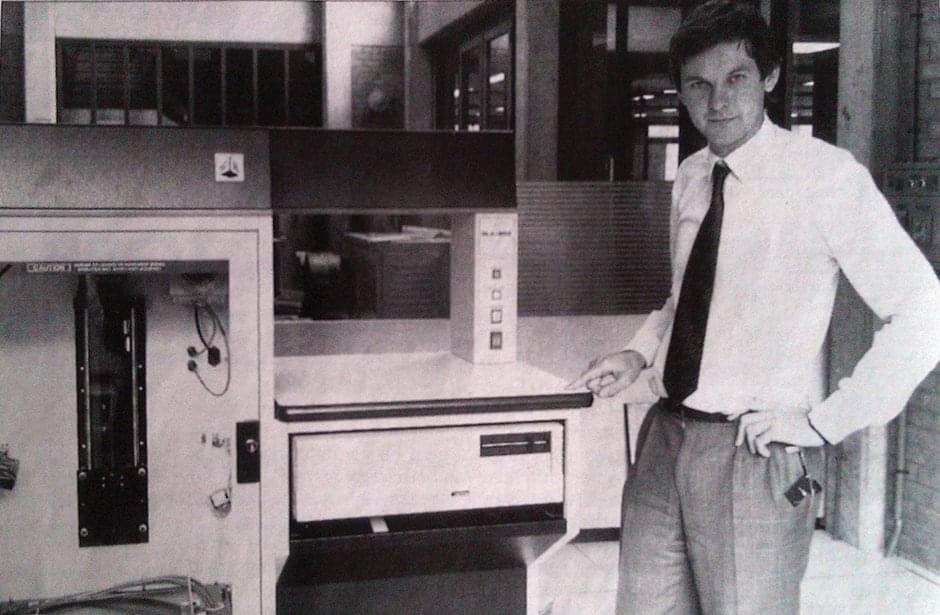
- In order to build single-piece stereolithography models with dimensions of more than two meters, Materialise has developed a unique technology: Mammoth stereolithography. The idea of producing large components without any gluing arose out of the growing demand for extremely fast and large prototypes of superior quality.
