Wie es funktioniert
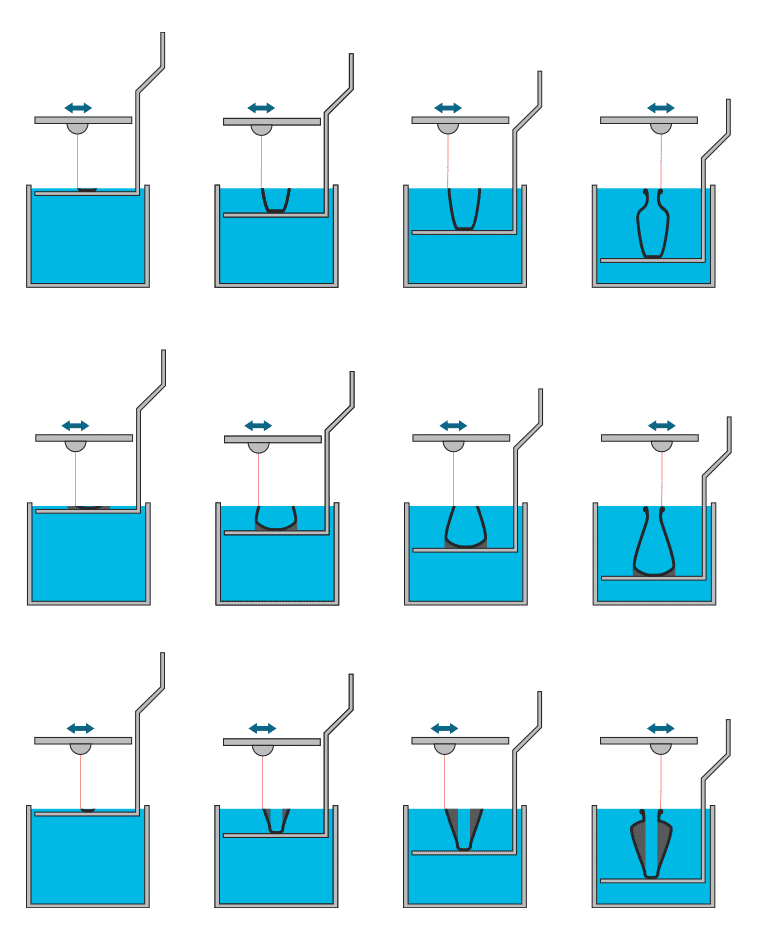
Auf Basis eines 3D-Modells wird Ihr Modell mit Hilfe einer Software aus dünnen Materialschichten aufgebaut. Wo nötig werden Stützstrukturen platziert um ausreichende Stabilität für Überhänge oder Hohlräume zu schaffen.
Der Druckprozess wird in einem großen Behälter durchgeführt, in dem zum Start eine dünne Schicht eines flüssigen Kunststoffs auf einer Bauplattform verteilt wird. Ein computergesteuerter Laser zeichnet die erste Schicht Ihres Modells auf den flüssigen Kunststoff, der in den bestrahlten Bereichen aushärtet. Die gedruckte Schicht wird anschließend mit der Bauplattform abgesenkt. Eine neue Kunststoffschicht wird auf der Oberfläche verteilt und die nächste Druckschicht des Modells mit dem Laser ausgehärtet. Dieser Vorgang wird bis zur Fertigstellung des Modells wiederholt. So wird das Objekt Schicht für Schicht mit dem Laser in die Flüssigkeit "gezeichnet", während die einzelnen Schichten während des Prozesses verfestigt werden.
Nach Abschluss des Druckvorgangs wird das Modell mit der Bauplattform aus dem Tank mit flüssigem Kunststoff gehoben und so von überschüssigem Material getrennt. Die Stützstrukturen werden anschließend manuell entfernt.
Materialien
Standardharz
- Lichtdurchlässig
- Leicht zu bemalen
- Sehr glatte, hochwertige Oberfläche
- Verwendbar für visuelle, nicht-funktionale Modelle
Graues Harz
- Leicht zu bemalen
- Mittlere mechanische Festigkeit
- Sehr glatte, hochwertige Oberfläche
- Verwendbar für große visuelle, nicht-funktionale Modelle
Mammutharz
- Leicht zu bemalen
- Mittlere mechanische Festigkeit
- Sehr glatte, hochwertige Oberfläche
- Verwendbar für große visuelle, nicht-funktionale Modelle
- Kann auch als Master für eine Form verwendet werden
Transparentes Harz
- Geeignet für (große) Modelle mit einer qualitativ hochwertigen, glatten Oberfläche und einem transparenten Look
- Ideal geeignet für besonders präzise Modelle und Vorfürmodelle mit eingeschränkter Funktionalität.
- Die Farbe des Materials ist transparent, jedoch nicht 100% kristallklar.
- Eingeschränkte Gestaltungsfreiheit auf Grund notwendiger Stützstrukturen
Wissenswertes
Schon gewusst?
- Stereolithografie leitet sich von den griechischen Wörtern Stereo (fester Körper), Litho (Stein) und Graphein (Schreiben) ab.
- Stereolithografie ist die älteste 3D-Druck Technologie
- Im November 1981 veröffentlichte Hideo Kodama vom Nagoya Municipal Industrial Research Institute (Nagoya, Japan) eine wissenschaftliche Arbeit mit dem Titel "Automatic Method for Fabricating a Three-Dimensional Plastic Model with Photo Hardening" (Automatisierte Methode zur Herstellung eines dreidimensionalen Kunststoffmodells durch photochemische Aushärtung). Kodama beschreibt drei grundlegende Methoden zur Herstellung von Kunststoffbauteilen durch das Aushärten von dünnen Schichten eines Photopolymers. Vermutlich schuf Kodama in seinen Experimenten das erste funktionsfähige additive Fertigungsverfahren der Welt.
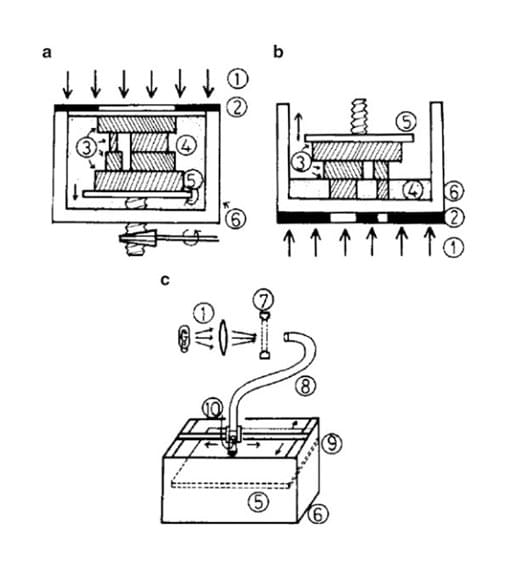
- Am 11. März 1986 wurde das Stereolithografieverfahren von Charles (Chuck) W. Hull patentiert. Er prägte zudem den Namen des Verfahrens im U.S. Patent 4,575,330, mit dem Titel "Apparatus for Production of Three-Dimensional Objects by Stereolithography" (Vorrichtung zur Herstellung dreidimensionaler Objekte durch Stereolithografie). Hull definierte Stereolithografie als das Verfahren, durch das fortlaufende Erzeugen dünner Schichten aus mittels UV-Strahlung aushärtbarem Material durch die beschriebene Vorrichtung, feste Objekte herzustellen.
- Materialise verwendet dieses Verfahren seit 1990.
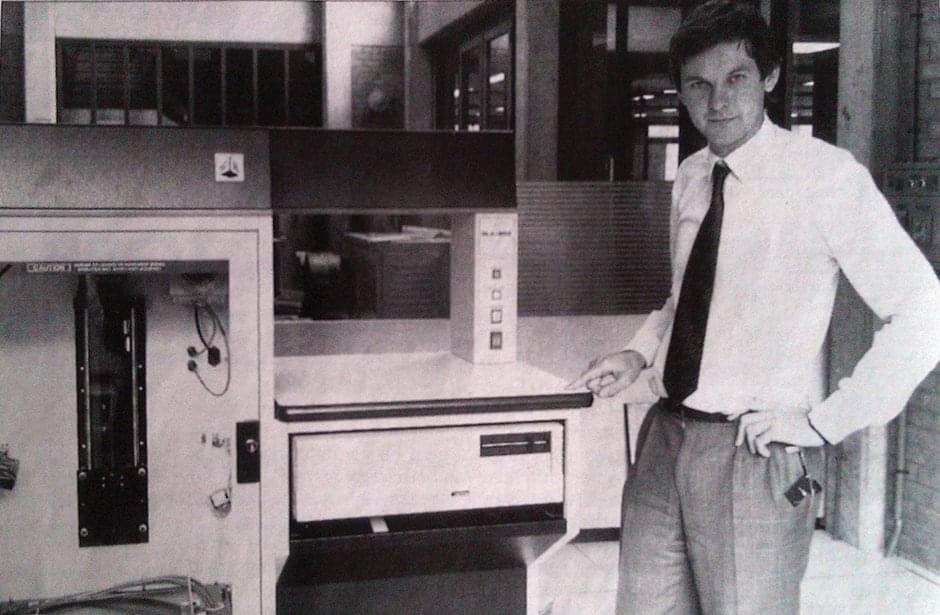
- Um Einzelteile mit Abmessungen von mehr als 2 Metern herstellen zu können, hat Materialise eine einzigartige Technologie entwickelt: Mammut-Stereolithografie Die Idee große Komponenten ohne notwendiges Kleben herzustellen, entstand durch die steigende Nachfrage nach sehr schnell verfügbaren und besonders großen Prototypen mit hervorragender Qualität.
