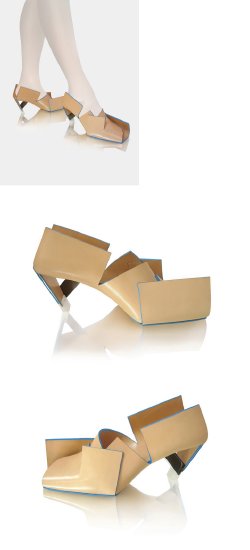
i.materialise interviews groundbreaking shoe designer Marloes ten Bhömer
In my mind there are only two shoe designers that are really revolutionizing shoe design. One is Rem D Koolhaas of United Nude and the other Marloes ten Bhömer. Both a are using cutting edge materials and design to make shoes contemporary and amazing again.
Marloes ten Bhömer is a lauded designer who has been called “one of the most promising designers of her generation”. She uses innovative production techniques, new materials and completely different ways of looking at form & function to redefine footwear. Marloes’ Rapidprototypeshoe, pictured below, is a great example of using 3D printing to create wearable footwear. We interviewed Marloes to find out more about her beautiful shoes.
Joris Peels: Why use 3D printing?
Marloes ten Bhömer: 3D printing is interesting to me on various levels.
It’s quite difficult to convince manufacturers to produce parts for products that are outside their usual industry. In my case I use production methods and materials that are rarely or not even used in the footwear industry. This makes (so far) for very niche market shoes and low volume production. With rapid manufacturing there are two advantages for me; I don’t have to convince anyone to produce parts for me and there are no extra set-up costs for low volume production or one-offs.
Next to this, I find it very interesting how rapid prototyping machines work. A “raw” material that is constructed into cured or sintered layers, making for a more or less structurally sound material and how to employ this is both interesting and challenging. There is also the obvious interest in the creation of build parts that can only be achieved with Rapid Manufacturing, their aesthetic possibilities and real time use (now and future) is really exiting.
JP: Is the shoe meant to fall apart? Is this an actual product?
Marloes ten Bhömer: The shoe is not meant to fall apart. For this shoe I have started looking into Rapid Manufacturing as a potential for real production of objects/shoes, not just prototypes. The concept of the shoe is based on the ability to produce a shoe in multiple materials in one go, however the shoe is designed in such a way, that it can be dismantled for the purpose of replacing parts. I have used the VeroBlack for the heel with the TangoBlack for the upper and sole part. VeroBlack might be too brittle for the heel, the TangoBlack seems to work well.
(Both VeroBlack and TangoBlack are Objet 3D printing materials made with the Polyjet process, we call them High detail resin and Rubber Like here on i.materialise)
JP: What was difficult about making it?
Marloes ten Bhömer: Apart from modeling the shoe, shoes and feet have amazing continuous curves which are quite difficult to model to match the exact size of the foot, the steep upright panels on the side of the shoe are a bit tricky for the machine (Objet Connex500) to achieve. Next will be testing a hard core on the inside of the panels or producing the shoe on it’s side, so the scaffold material supports the panels. Hopefully this will be happening soon.
At the moment I am most interested in developing objects for use (not for prototyping) with Rapid Manufacturing. Within this I see an interesting design challenge; I think that the way forward in design in terms of sustainability and use is that parts can easily be replaced or updated. There are quite a few examples of Rapid Prototyped hinges, but the build tolerance seems to be an issue when designing parts that are pressure fit for example. I would be interested in designing systems that allow an object to be build in parts without (too much) assembly and easy dismantle.
Of course this idea is based on imagining concepts without too much insider knowledge and there are of course other concepts that can be tested within shoe design as well. A shoe is such a small object with a need for a wide variety of material properties such as, good abrasion, air ventilation, flexibility, load baring, torsion etc. In any case, lots to be tested and developed and outcomes that can be used within other industries as well.
Thank you so much for doing this interview Marloes. Below is a gallery of some of the other innovative shoes Marloes makes. You can see even more on her site.
Recommended Articles
No related posts.